Description
High Speed 0.16mm 0.18mm 0.20mm Molybdenum Wire For WEDM Wire Cutting Mahine High Efficientcy 2000m Wire-cut Molybdenum Wire
Features:
1. This molybdenum product has super strength of extension.
2. It features excellent oxidation and corrosion resistance in a variety of harsh thermal and corrosive environments.
3. Molybdenum wire is stable and high precision in cutting. It is not easy to fracture and has long operating life.
4. The molybdenum product is in vacuum package and accurate in measuring. It can preserve for a long time.
5. Its melting point is 2620°C 4748 °F, featuring good electrical and thermal conductivity.
Applications:
1. Circles the filament core, the support wire, the lead-out wire, the electronics grid and so on.
2. The support silk, the lead-out wire guide rod, the electricity vacuum components, the heater element, the high temp electric resistance furnace gives off heat the material and so on.
3. For EMD wire cut, high tensile strength, small elongation ratio, good stability, high cutting precision.
Parameters:
Dinameter: 0.15mm, 0.16mm, 0.18mm, 0.20mm
Wire length: 2000m, 3000m
Purity: >99.99
Material: Molybdenum /Mo
Broken wires related to molybdenum wires
1. Tension and threading speed
1 Increasing the tension of molybdenum wire can reduce the impact of wire vibration, thus improving the precision and cutting speed, and significantly reducing wire breakage. Generally, it is considered that the tension is 12-15N.
2 The increase of wire speed is beneficial to the molybdenum wire to bring the working fluid into the discharge gap of the workpiece with larger thickness, ensuring the elimination of the corrosion products and the stability of the EDM. However, if the wire speed is too high and the molybdenum wire shakes seriously, the stability of processing will be damaged, the processing accuracy and surface roughness will become worse, and wire breakage will be easily caused. When the wire speed is too low, the wire is easy to break due to large loss, so it is better to be less than 10m/s in general experience.
Broken wire related to guide wire structure
1. Broken wires related to the thread carrier
1 The different axes of the inner and outer circles of the thread carrier will produce unbalanced inertia, which will easily lead to wire breakage due to wire stacking during operation.
2 The shaft, bearing and other parts of the silk conveying cylinder often have clearance due to wear, which is easy to cause wire jitter and wire breakage.
3 If the high-frequency power supply is not cut off during the reversing of the screw barrel, the molybdenum wire will burn in a short time due to high temperature. Therefore, it is necessary to check whether the travel switch at the rear end of the screw barrel fails whether the relay controlling the high-frequency is damaged.
4 Keep the thread carrier and guide wheel rotating flexibly, otherwise the vibration of the wire guide system will cause wire breakage during the round-trip operation.
5 It is necessary to adjust the limit stop at the rear end of the thread carrier to prevent the thread from breaking due to the limit stroke of the thread carrier.
6 The machine shall be stopped shortly after the change to prevent the drive parts from being damaged and molybdenum wires from being pulled off by the wire conveying cylinder due to inertia overtravel.
2. Broken wire related to guide wheel and conductive block
1 If the guide wheel and conductive block have grooves due to wear, or the guide wheel bearing has gaps due to wear, it is easy to cause molybdenum wire jitter and wire breakage.
2 It should be ensured that the molybdenum wire and the conductive block, the processing workpiece and the worktable are in good contact, otherwise the high-frequency power cathode can not be connected with the molybdenum wire or cause poor contact.
Wire breakage during machining thick workpieces
Molybdenum coil
Thick workpieces generally refer to workpieces with thickness greater than 100mm. The main reasons for wire breakage are:
1. Broken wire at the beginning of cutting
This is because the molybdenum wire is outside the workpiece during initial cutting, and the distance between the upper and lower guide wheels is large, which causes the molybdenum wire to pull and shake, making the gap between the molybdenum wire and the workpiece unstable, which is easy to form arc discharge, so that the arc is concentrated in a certain section, which will cause wire breakage. In EDM, arc discharge is the main factor that causes the cathode corrosion damage.
2. Wire breakage during cutting
When the molybdenum wire cuts into the workpiece, due to the narrow kerf and the difficulty of emulsion penetration, it is not easy to remove the electric erosion carbon black and metal in the kerf, which worsens the processing conditions. Secondary and tertiary electric discharge machining is generated in the kerf, which causes the kerf to become wider and the gap to enter into a poor state, causing the pulse to form an arc discharge, causing wire breakage.
3. Broken wire at the end of cutting
In addition to the above reasons, the wire breakage after fast cutting is still several millimeters or even tens of microns away, and the wire breakage caused by the deformation caused by the dead weight of the workpiece or the internal stress of the workpiece material, the solution is: simple jigs and fixtures can be self-made, and the material factory can make necessary heat treatment before processing.
Wire breakage related to working fluid
1. When the working fluid turns black, its comprehensive performance will become worse, which is very easy to cause wire breakage. Therefore, it is necessary to observe its color and smell its smell frequently, and replace it in time in case of any abnormality, so as to maintain a certain dielectric capacity of the working fluid. In particular, when machining hard alloy, there are many erosions, which easily lead to poor permeability and fluidity of the working fluid, resulting in poor chip removal.
2. How to identify saponification solution
1 Wrap a little new molybdenum wire and try to cut it on the workpiece for about 1 hour. Observe the color of the molybdenum wire. If the molybdenum wire is gray white, the coolant can cut thinner workpieces, such as gray white mixed with black spots or black stripes. The diameter of the black stripes becomes significantly thinner, so it is necessary to replace the working fluid.
2 Look at arcing and path current. Start the wire carrier, manually force the high-frequency current to connect, and make the molybdenum wire slowly close to the workpiece. Do not touch the workpiece. The spacing is about 1-1.5mm. At this time, there should be no sparks. Then cool the workpiece to make the distance between molybdenum wire and workpiece form a liquid path. If there is a spark or the reading value of the ammeter is increased by more than 10mA on the basis of the original no-load about 30mA for no-load, the working fluid can no longer be used at this time.
Broken wires related to electrical parameters
1. Select reasonable electrical parameters according to the thickness of the workpiece, and open the pulse interval to facilitate the discharge of molten metal particles. At the same time, the no-load voltage of the peak current should not be too high, otherwise, the single pulse energy will become larger, the cutting speed will be accelerated, and it is easy to produce concentrated discharge and arc, causing wire breakage. Generally, the no-load voltage is about 100V.
2. Select the appropriate discharge gap according to the thickness of the workpiece. If the discharge gap is too small, it is easy to cause short circuit, and it is not conducive to cooling and removal of electric erosion; Excessive discharge gap will affect surface roughness and machining speed. When cutting workpieces with large thickness, large pulse width current should be selected as far as possible, and discharge gap should also be correspondingly larger generally greater than 0.02mm to enhance chip removal effect and improve cutting stability
Broken wires related to high-frequency power supply
1. If the peak value of short circuit current is too large, that is, the number of power amplifier tubes input is too large, which exceeds the current that the molybdenum wire can withstand, the molybdenum wire will overheat and brittle fracture due to excessive fatigue.
2. If the negative wave of high-frequency pulse is too large, the negative wave of the pulse will directly corrode the molybdenum wire, increasing the wire loss, reducing the service life of the wire, and causing wire breakage in a short time.
3. If the pulse width and pulse interval are not properly selected, when machining the workpiece with large thickness, the pulse width is too large, which will cause the discharge point concentration in the discharge gap and burn the molybdenum wire; If the pulse interval is too small, the erosion in the gap cannot be fully discharged, the deionization is not sufficient, and the wire is easy to break. At this time, burn marks i.e. black spots can be clearly seen on the molybdenum wire.
Broken wires related to table movement
1. The cutting accuracy of the workpiece is guaranteed by the screw rod, and the clearance between the screw rod and the nut is eliminated by the spring. If the screw rod is poorly lubricated or the spring force is insufficient, the worktable will move at an uneven speed. In this case, the high-frequency current will cause frequent short circuits. If the fault is not eliminated in time, the wire will be broken.
2. When adjusting the frequency conversion tracking speed, try to make the feed speed approximately equal to the working etching speed, so that the pulse utilization rate is high, the processing speed is fast, and the processing state is stable. The feed speed is too high, the short circuit is frequent, and the wire aging is fast. It can be seen from the ammeter that the processing current is large; If the processing speed is too low and the feed speed is too slow, it is easy to make the discharge gap unstable, generate transient arc discharge, and easily burn the molybdenum wire.
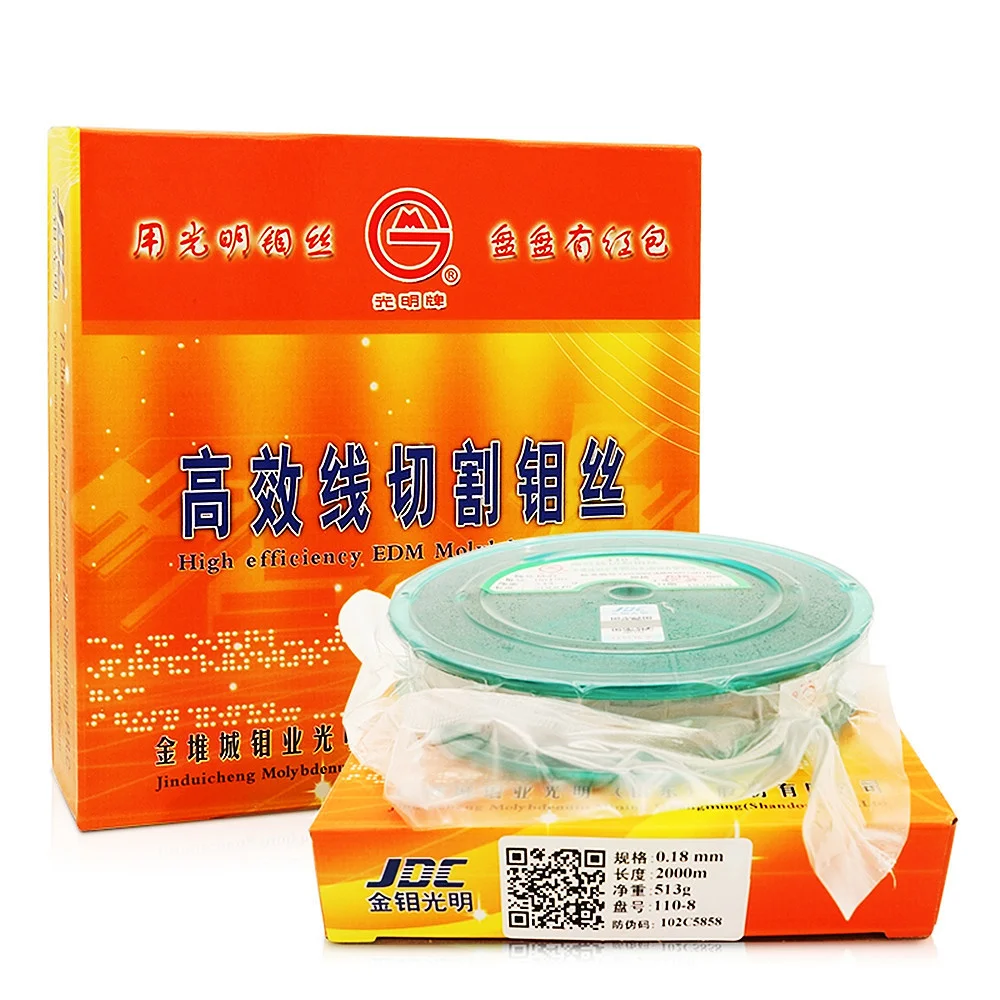
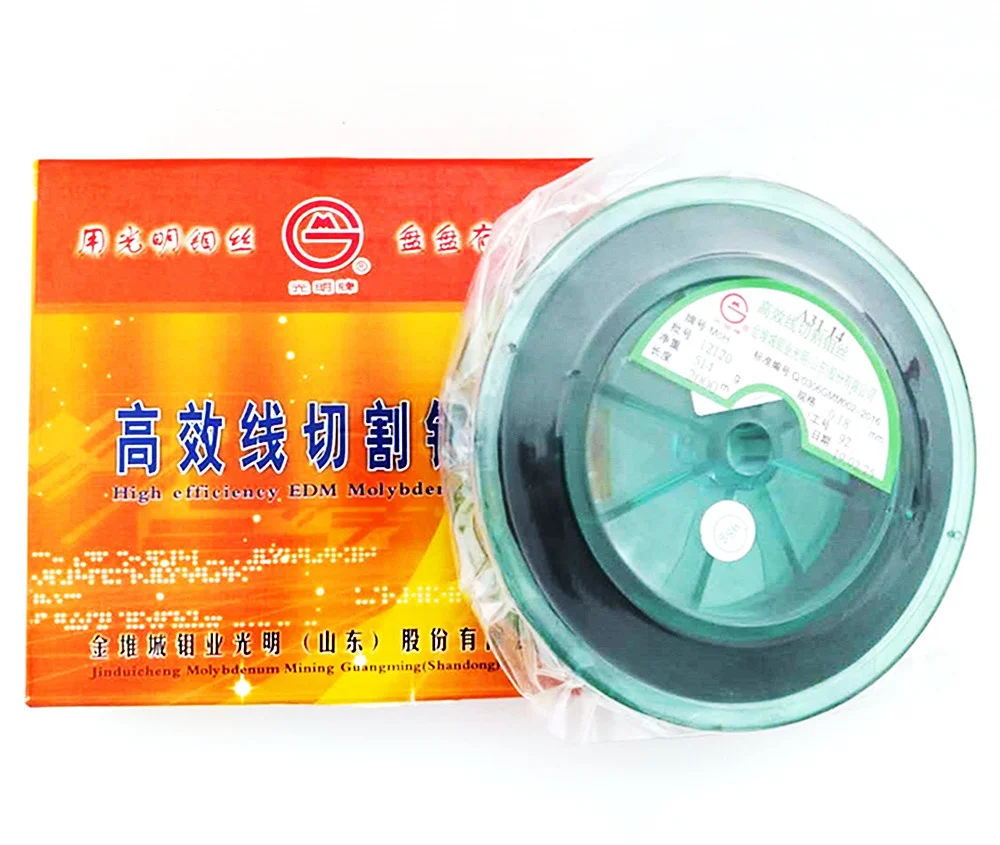
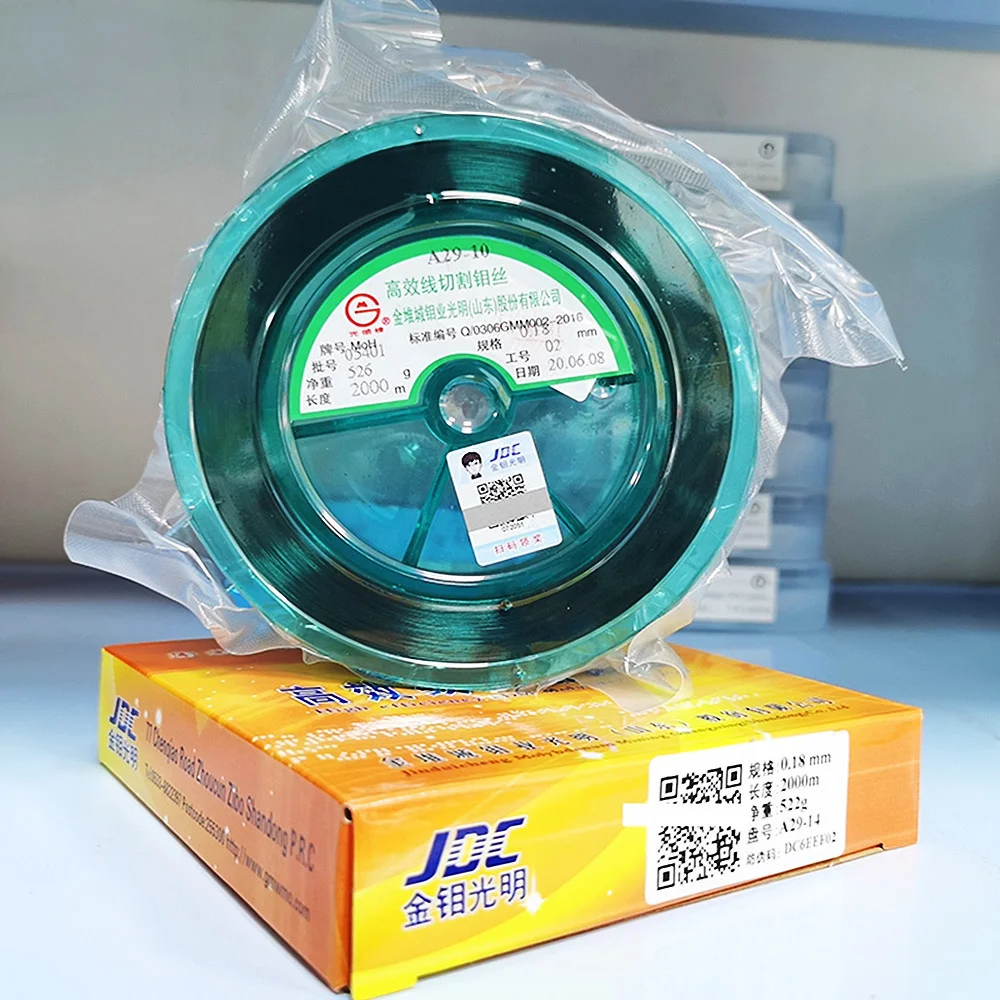


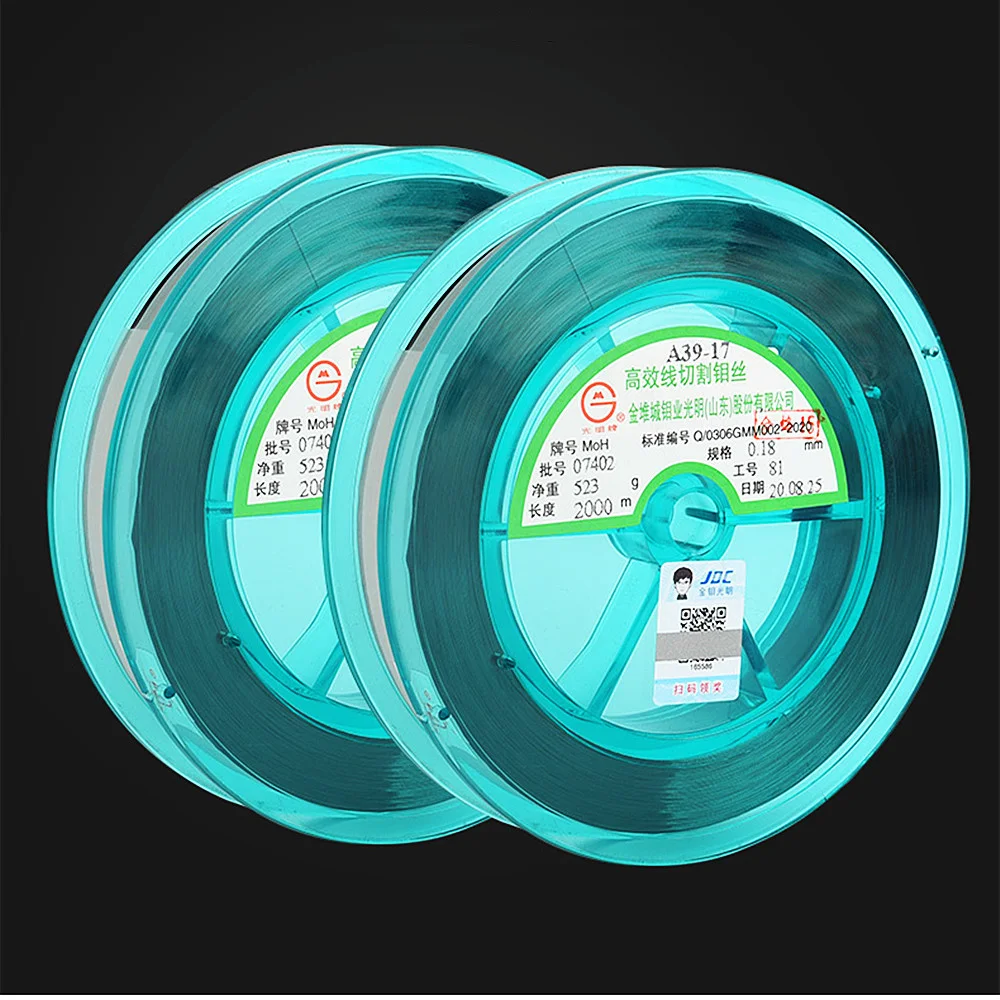

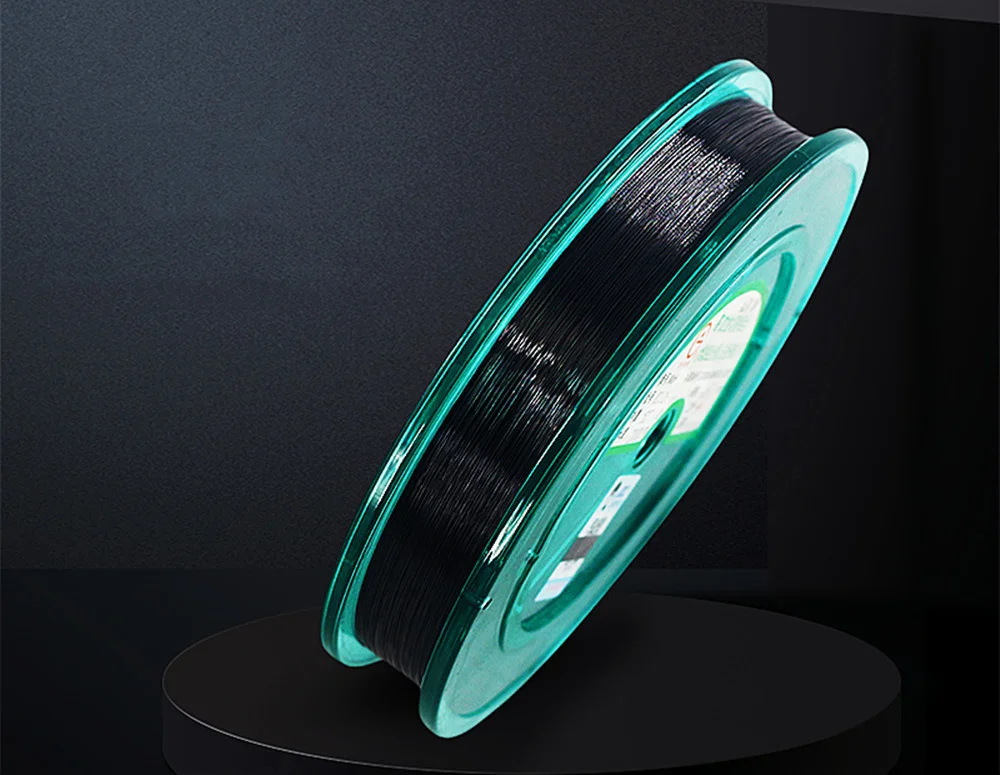


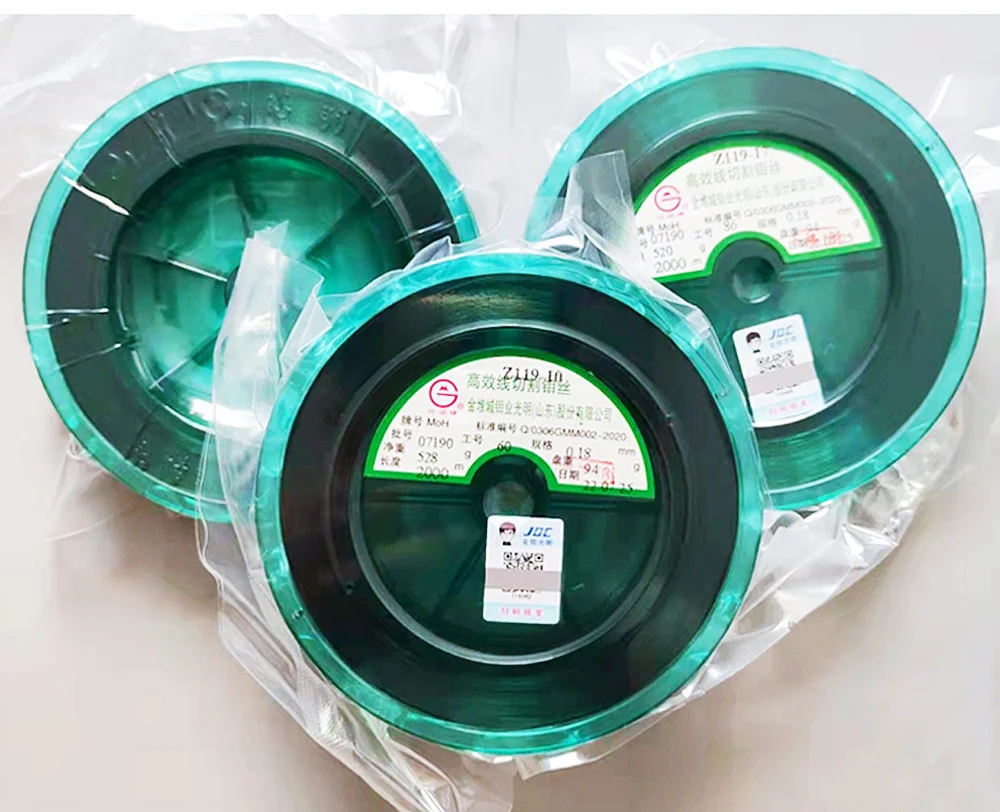
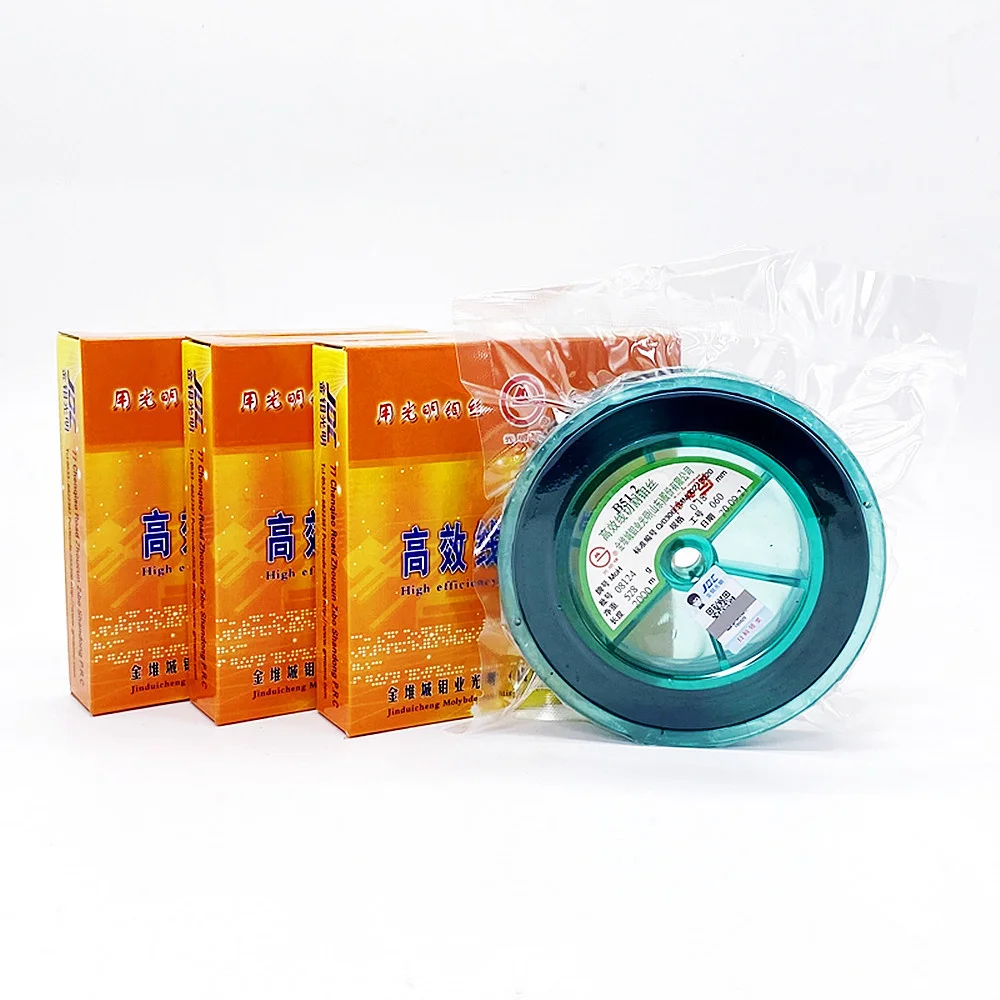

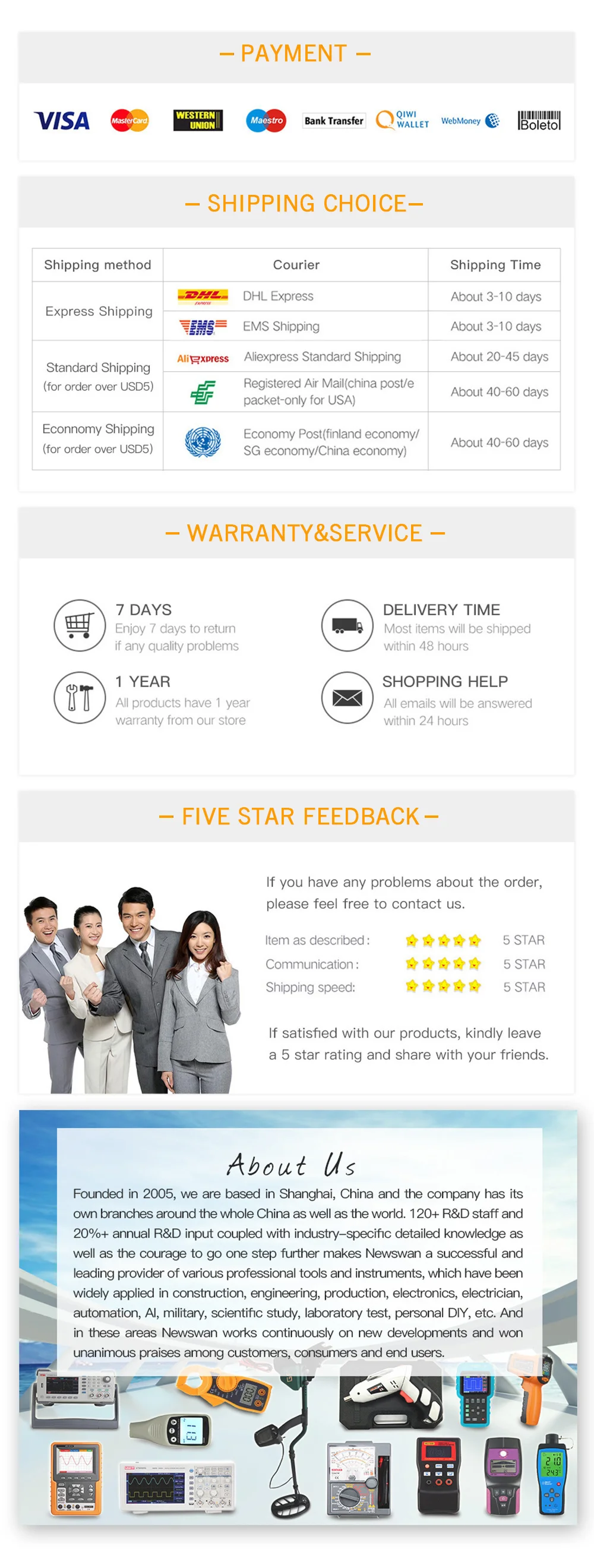
Reviews
There are no reviews yet.